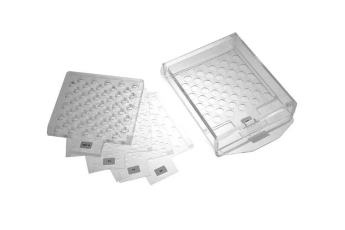
Accurately counts coated and uncoated tablets and capsules. Tablets up to a diameter of 1/2″ and capsules up to 3/4″ long can be counted using a range of 5 interchangeable perforated plates. Perspex construction aids visual checking and easy cleaning. Full withdrawal dispenses 50 to 100 tablets.